Kako so narejene karbidne rezila?
Carbide rezila so cenjena zaradi izjemne trdote, odpornosti proti obrabi in sposobnosti vzdrževanja ostrine v daljšem obdobju, zaradi česar so idealni za rezanje živih materialov.
Carbide rezila so običajno narejena s postopkom, ki vključuje sintranje volframovega karbida v trdno obliko, čemur sledi oblikovanje in zaključek rezila. Tu je korak za korakom pregled, kako na splošno nastajajo karbidne rezila:
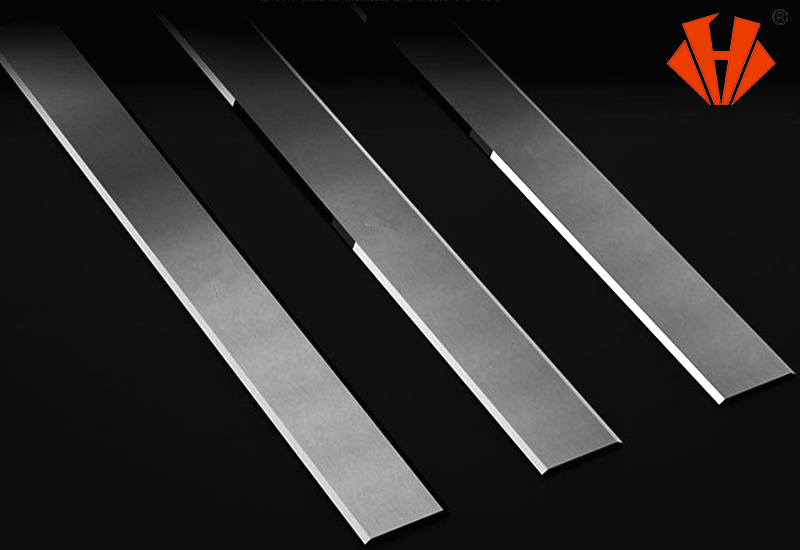
1. Priprava surovin
- Volframovi karbidPrah: Primarni material, ki se uporablja v karbidnih rezilih, je volframovi karbid (WC), ki je gosta in trda spojina volframa in ogljika. V prahu oblike volframovega karbida se meša s kovino vezivo, običajno kobalta (CO), da pomaga pri postopku sintranja.
- Mešanje v prahu: Prah in kobalt volframovega karbida se mešata skupaj, da tvorita enakomerno zmes. Mešanica je skrbno nadzorovana, da se zagotovi pravilno sestavo za želeno trdoto in žilavost rezila.
2. Stiskanje
- Oblikovanje: Zmes v prahu postavimo v kalup ali matrico in stisnemo v kompaktno obliko, ki je groba obris rezila. To se običajno izvaja pod visokim pritiskom v postopku, ki se imenujeHladno izostatično stiskanje (CIP) or enoosno stiskanje.
- Oblikovanje: Med stiskanjem se oblikuje groba oblika rezila, vendar še ni popolnoma gosta ali trda. Tisk pomaga kompaktno mešanico v prahu v želeno geometrijo, kot je oblika rezalnega orodja ali rezila.
3. Sintranje
- Visokotemperaturno sintranje: Po stiskanju rezilo opravi postopek sintranja. To vključuje segrevanje stisnjene oblike v peči pri temperaturah, ki so običajno med1.400 ° C in 1.600 ° C.(2552 ° F do 2912 ° F), zaradi česar se praškasti delci zlijejo skupaj in tvorijo trden, gost material.
- Odstranjevanje veziva: Med sintranjem se obdela tudi kobalt veziva. Pomaga delcem volframovega karbida, ki se držijo drug drugega, vendar po sintranju pomaga tudi, da rezilu daje končno trdoto in žilavost.
- Hlajenje: Po sintranju se rezilo postopoma ohladi v nadzorovanem okolju, da se prepreči razpokanje ali izkrivljanje.
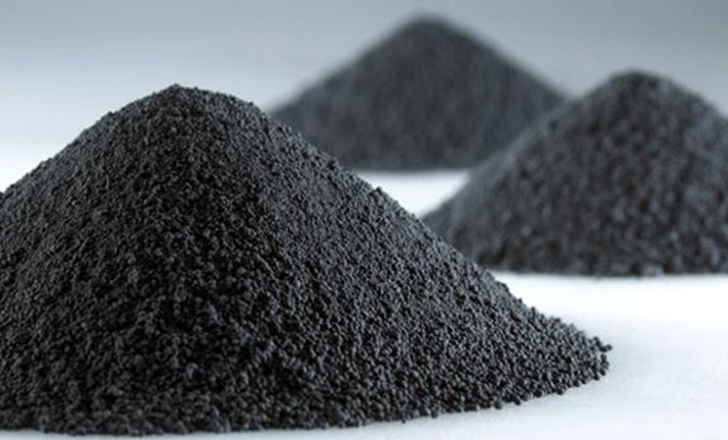
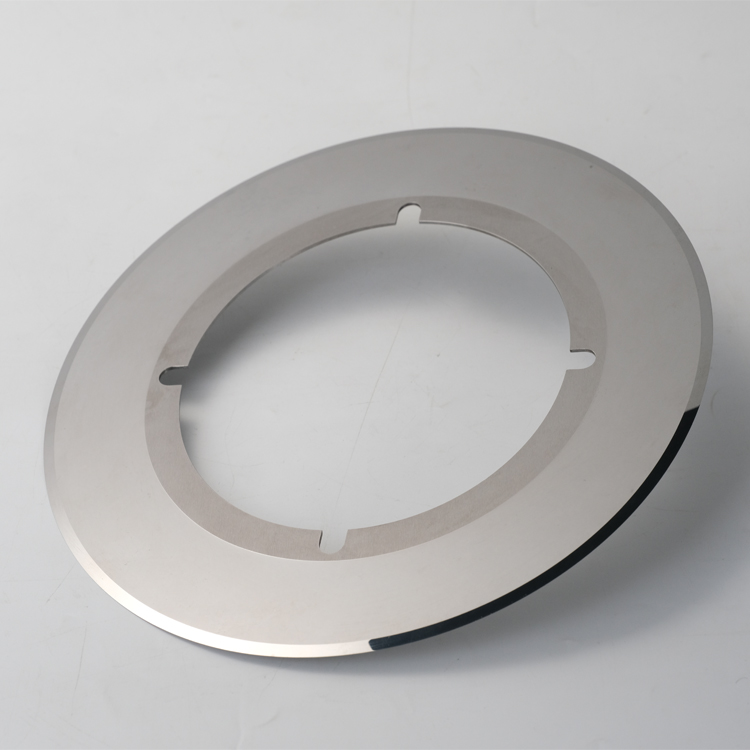
4. Brušenje in oblikovanje
- Brušenje: Po sintranju je karbidno rezilo pogosto preveč grobo ali nepravilno, zato je na podlagi natančnih dimenzij z uporabo specializiranih abrazivnih koles ali brusilnih strojev. Ta korak je bistven za ustvarjanje ostrega roba in zagotavljanje, da rezilo ustreza potrebnim specifikacijam.
- Oblikovanje in profiliranje: Glede na aplikacijo lahko rezilo nadaljuje z oblikovanjem ali profiliranjem. To bi lahko vključevalo mletje specifičnih kotov na rezalnem robu, nanašanje premazov ali natančno nastavitev celotne geometrije rezila.
5. Dokončni tretmaji
- Površinske prevleke (neobvezno): Nekatere karbidne rezila dobijo dodatne obdelave, kot so prevleke materialov, kot je titanov nitrid (kositer), za izboljšanje trdote, odpornost na obrabo in zmanjšanje trenja.
- Poliranje: Za nadaljnje izboljšanje zmogljivosti je mogoče rezilo polirati, da dosežemo gladko, dokončano površino, ki zmanjša trenje in izboljša učinkovitost rezanja.
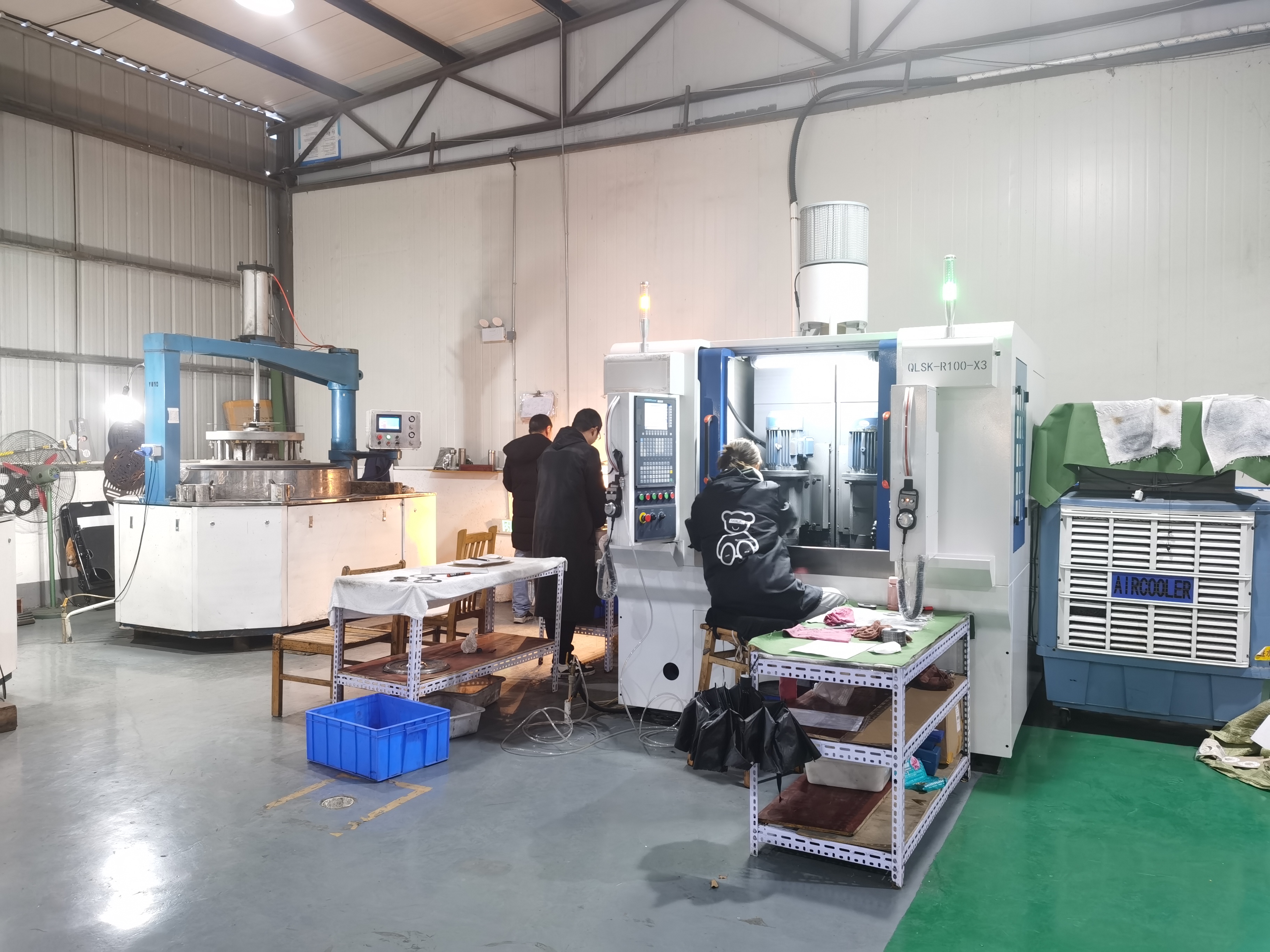
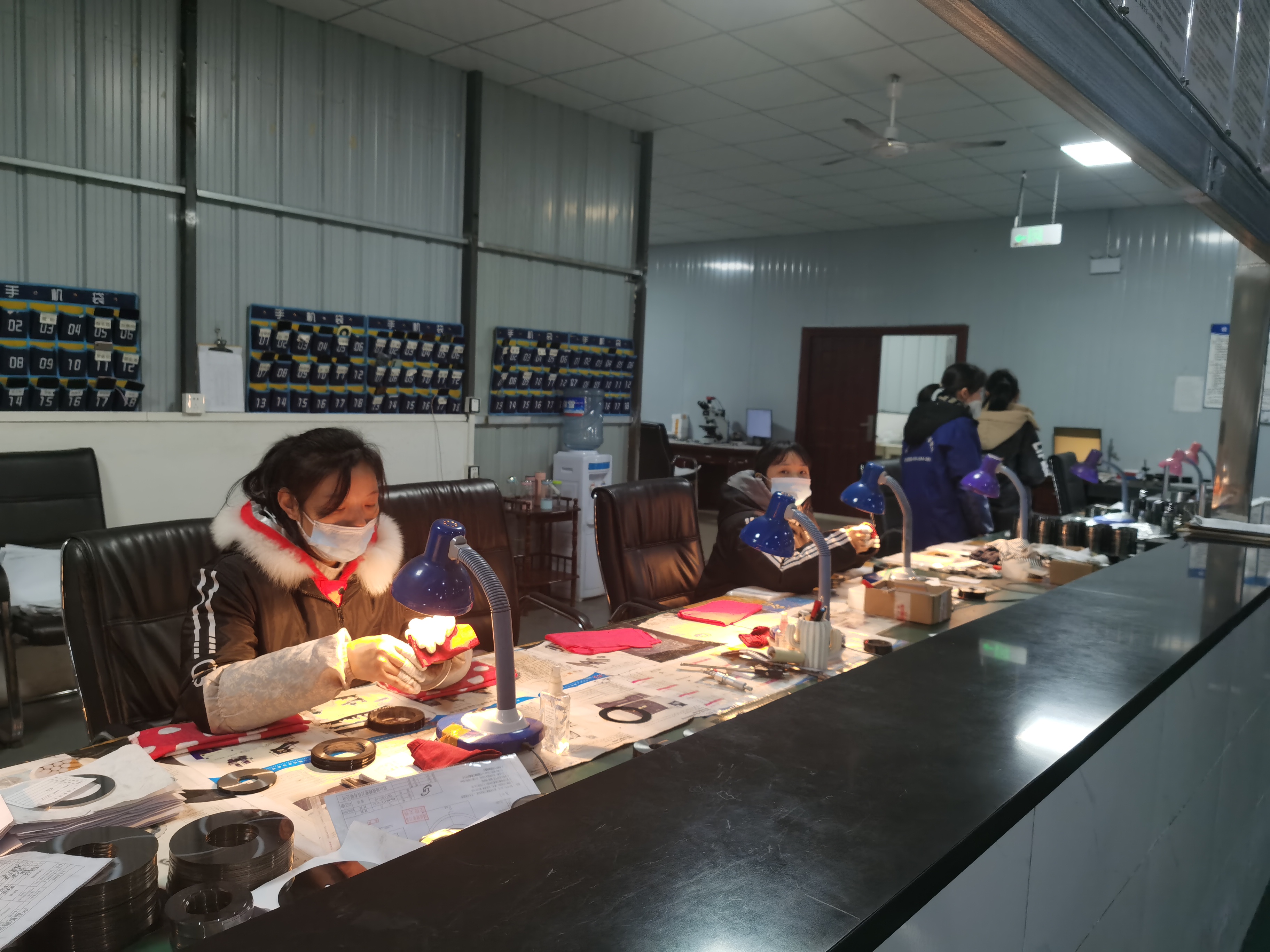
6. Nadzor kakovosti in testiranje
- Testiranje trdote: Trdota rezila se običajno preizkusi, da se zagotovi potrebne specifikacije, s skupnimi testi, vključno s testiranjem trdote Rockwell ali Vickers.
- Dimenzijski pregled: Natančnost je ključnega pomena, zato se dimenzije rezila preverijo, da se zagotovi natančne tolerance.
- Testiranje uspešnosti: Za posebne aplikacije, na primer rezanje ali rezanje, lahko rezilo opravijo testiranje v resničnem svetu, da se zagotovi, kot je predvideno.
Huaksin je cementiral karbid Ponuja vrhunske nože in rezila za volframove karbide za naše stranke iz različnih panog po vsem svetu. Rezila je mogoče konfigurirati tako, da ustreza strojem, ki se uporabljajo pri skoraj vseh industrijskih aplikacijah. Materiali rezila, dolžina roba in profili, obdelave in premaze je mogoče prilagoditi za uporabo s številnimi industrijskimi materiali
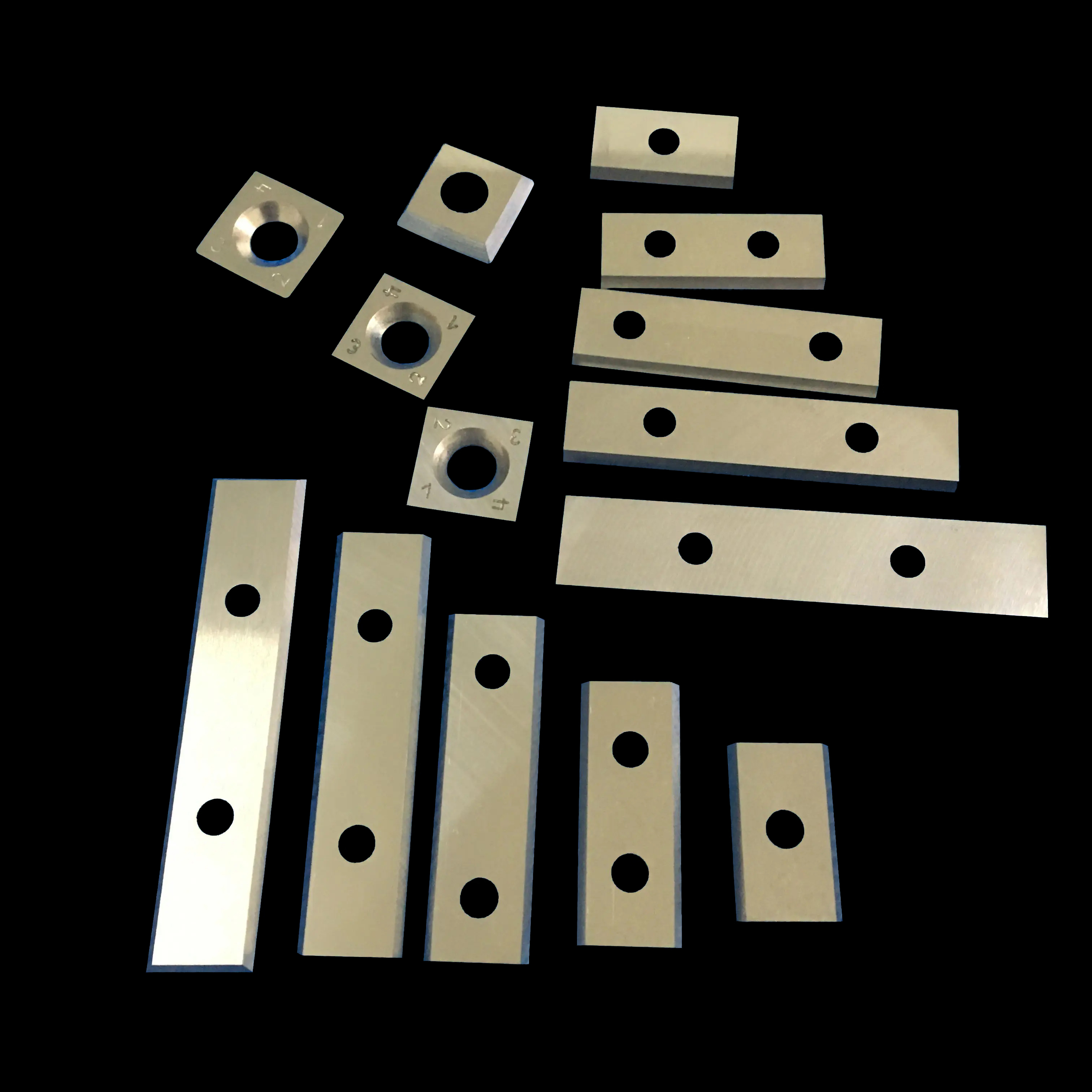
Ko rezila opravijo vse kakovostne preglede, so pripravljeni za uporabo v različnih industrijskih aplikacijah, na primer pri obdelavi kovin, embalaži ali drugih operacijah rezanja, kjer sta visoka odpornost na obrabo in ostrina bistvenega pomena.
Čas objave: november-25-2024